Recognizing the Fundamentals of Welding Inspection to Make Certain High Quality and Safety
In the world of modern-day design, welding assessment stands as a cornerstone for making certain both the top quality and safety of structural productions. What are the nuances of these assessment approaches that make them crucial for maintaining architectural stability?

Relevance of Welding Inspection
In the realm of commercial fabrication, the importance of welding assessment can not be overstated. Welding inspection plays a vital duty in making sure the integrity, security, and durability of welded structures. Given the diverse applications of welding in markets such as construction, automobile, aerospace, and shipbuilding, the need for rigid quality assurance actions is critical. Correct assessment makes sure that welds meet defined codes and standards, which is crucial for protecting against architectural failings that might cause catastrophic repercussions.
The process of welding naturally includes intricate variables, including temperature level, material properties, and environmental conditions, all of which can affect the top quality of the weld. A complete inspection identifies defects such as splits, porosity, and incomplete combination, which can jeopardize the toughness and dependability of the weld. By spotting these issues early, corrective activities can be taken, consequently minimizing the risk of failing and linked prices.
Additionally, welding examination adds to regulative conformity, as many markets are governed by stringent safety and security standards and guidelines. Failure to comply with these laws can result in economic fines and lawful responsibilities. Ultimately, welding assessment not just safeguards physical structures but additionally promotes and shields human lives sector reputations.

Key Welding Evaluation Methods
Although welding inspection is vital to making sure the top quality and safety and security of welded structures, it is the particular approaches employed that determine the effectiveness of the assessment procedure. Trick welding inspection methods can be extensively classified into non-destructive screening (NDT) and devastating screening.
Radiographic and ultrasonic screening are more advanced techniques that enable inspectors to examine the inner integrity of the weld. Ultrasonic testing utilizes high-frequency audio waves to find gaps, while radiographic testing uses X-rays or gamma rays to generate a photo of the weld's inside. Magnetic bit testing and fluid penetrant screening are surface area inspection approaches made use of to situate surface area and near-surface problems. In comparison, harmful testing approaches involve physically reducing the weld or damaging to assess its mechanical residential properties. These thorough evaluation approaches make sure that welds meet sector criteria and safety needs, consequently ensuring architectural honesty and performance.
Duty of Licensed Examiners
Certified examiners play a pivotal duty in the welding examination process, guaranteeing that all welds follow rigid market criteria and safety and security laws. Their proficiency is vital in determining flaws or abnormalities that might jeopardize the architectural integrity of a weld. By carefully examining each weld, certified assessors aid stop prospective failings that might result in costly repair work or unsafe accidents.
To become qualified, inspectors must undergo strenuous training and testing, which familiarizes them with different welding techniques, products, and screening approaches. This detailed expertise permits them to examine weld quality successfully and make informed judgments regarding their safety and reliability. Licensed assessors are proficient in analyzing specifications and plans, making sure that the welding job straightens with the project's layout needs.
An integral component of their duty is to record their findings thoroughly, providing a detailed record of the evaluation procedure. Their contribution is essential in keeping high levels of top quality and safety and security in welding procedures.

Devices Made Use Of in Welding Assessment
Welding assessors rely on a range of specialized devices to perform their responsibilities properly, guaranteeing each weld fulfills the necessary criteria. Among these devices, aesthetic assessment aids like multiplying glasses and mirrors are basic, enabling inspectors to carefully examine welds for surface flaws such as cracks, porosity, and undercut. Calipers and fillet weld determines are vital for gauging weld dimensions to verify conformity with design specs.
Advanced tools prolong past visual aids, consisting of non-destructive testing (NDT) devices. Ultrasonic testing tools are essential in detecting subsurface flaws, using audio waves to disclose interior suspensions without jeopardizing the weld's stability. Radiographic screening utilizes X-rays or gamma rays to catch pictures of a weld's interior, highlighting possible flaws.
Magnetic fragment testing is another vital device, specifically try this website for finding surface and near-surface interruptions in ferromagnetic products. By using magnetic areas and ferrous particles, inspectors can determine imperfections that could otherwise be unnoticeable.
Dye penetrant evaluation is commonly utilized for non-ferrous products, giving a contrast-enhanced visual check for surface-breaking problems. Welding Inspection Madison. Together, these devices allow welding inspectors to comprehensively evaluate weld quality, making sure security and integrity in various applications across sectors
Making Certain Structural Integrity
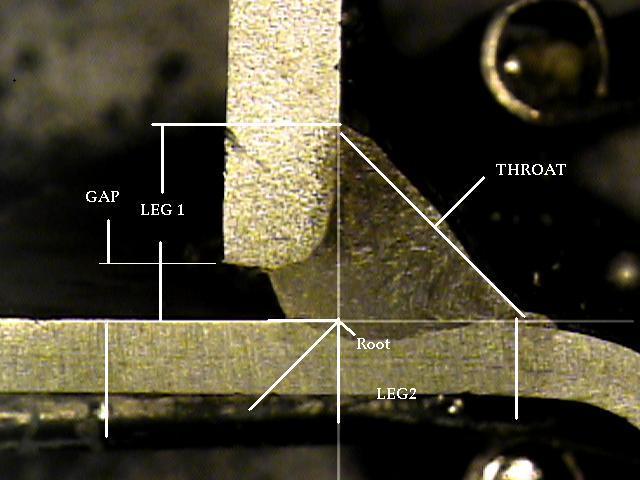
Welding procedures need to comply with well established requirements and navigate to this website codes, such as those defined by the American Welding Culture (AWS) or the International Company for Standardization (ISO) These guidelines ensure that the welds can endure operational stress and anxieties and environmental aspects. Certified and accredited welders play a crucial duty in this process, as their knowledge guarantees that techniques are applied appropriately, lessening defects such as cracks, porosity, and insufficient combination.
Post-weld inspection is an additional necessary element of validating structural integrity. These evaluations confirm that the welds fulfill the called for high quality criteria, providing guarantee of their toughness and dependability.
Final Thought
The basics of welding examination are vital for preserving the top quality and safety and security of welded frameworks. By applying vital evaluation methods, such as visual assessments and non-destructive screening, possible problems go right here that could jeopardize structural integrity are determined. Qualified examiners are vital in making certain compliance with sector standards and reliable communication among stakeholders. Making use of specialized devices better improves the inspection procedure, eventually protecting human lives and lengthening the life expectancy of welded building and constructions.
Welding inspection plays a critical duty in making certain the integrity, security, and durability of bonded structures.Although welding inspection is essential to ensuring the high quality and security of bonded frameworks, it is the certain techniques utilized that figure out the performance of the examination procedure. Secret welding evaluation approaches can be extensively classified into non-destructive screening (NDT) and devastating testing.Licensed examiners play a pivotal role in the welding examination procedure, ensuring that all welds abide with stringent market standards and safety laws.The principles of welding evaluation are vital for maintaining the top quality and safety and security of welded structures.